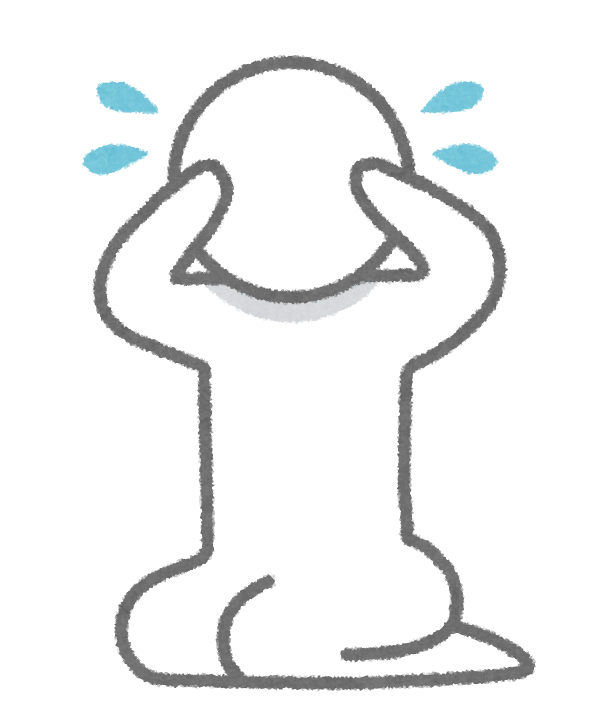
2024/03/18更新 人的要因とはヒューマンエラーのことです。エラーの6割はヒューマンエラーによるものとも言われていますが、このエラーはなぜなぜ分析においても避けて通れません。
ここではヒューマンエラー、人的要因についての考え方を紹介します。
無視することができない人的要因
エラーの6割が人的要因であるならば、この6割は無視することができません。
人以外に焦点を当ててなぜなぜ分析を実施する場合、この人的要因をどのように考えれば良いのでしょうか。
人はエラーを望んでいる訳ではない
前提として、エラーは行動の結果として現れるもので人はエラーを望んでいる訳ではないと言うことです。
望まない結果を生まないためにはどうしたら良いのかについて、なぜなぜ分析を通して考えることになります。
「認知」「判断」「行動」から考える
人的要因について考える場合は、「認知」「判断」「行動」のどのタイミングで「あるべき姿」から異なってしまったのかに注目します。
「あるべき姿」とは、作業標準などに基づいて作業したときの模範となる姿のことを言います。どのタイミングで異なってしまったかによって再発防止策を考える必要があるからです。
そこで、製品出荷を想定して考えてみます。
想定1
認知 | 判断 | 行動 | |
---|---|---|---|
あるべき姿 | 製品Aの出荷があることを認知する | 製品倉庫1から製品Aを取り出すして出荷する必要があると判断する | 製品倉庫1から製品Aを取り出して出荷する |
作業者 | 製品Aの出荷があることを認知する | 製品倉庫1から製品Aを取り出して出荷する必要があると判断する | 製品倉庫1から製品Aを取り出して出荷する必要があったにもかかわらず、隣に置いてあった製品Bを取り出して出荷してしまった |
想定1では、作業者があるべき姿から異なってしまったのは「行動」のところです。
製品Aを取り出すはずが隣に置いてあった製品Bを取り出して出荷してしまいました。
なぜ作業者が製品Bを取り出してしまったのか聞き取りを行ってみないことには真因を確認できませんが、これを単に人的要因として片づけてしまうのは会社にとっても不利益となります。
想定ではありますが、隣に置いてあった製品Bを取り出したことから事前にいくつかの要因が推測できます。
2. 製品Aと製品Bの外観が似ていた。
3. 作業者が慌てて作業していた。
新たに製品開発を行うとき、新たに作業場を設けるときなどでは当然のことながらリスクマネジメントとしてリスクを想定して事前に対策を講じる必要があります。
リスクの想定が充分でない場合には異常として現れるときがあり、これは管理者側(管理監督者側)の責任と考えます。
作業を詳しく理解していれば作業場の問題点が想定できるため、おおよそのリスクは回避できると思います。
・計量する。
・記録用紙に計量値を記入する。
・計量値が指定された範囲内であることを確認する。
・製品ラベルを確認する。
・パレットに載せる。
※この作業を1人で55秒以内に行う。
・計量する。
・記録用紙に計量値を記入する。
・計量値が指定された範囲内であることを確認する。
・パレットに載せる。
※この作業を1人で55秒以内に行う。
想定2
認知 | 判断 | 行動 | |
---|---|---|---|
あるべき姿 | 製品Aの出荷があることを認知する | 製品倉庫1から製品Aを取り出すして出荷する必要があると判断する | 製品倉庫1から製品Aを取り出して出荷する |
作業者 | 製品Aの出荷があることを認知する | 製品倉庫2から製品Aを取り出して出荷する必要があると判断する | 製品倉庫1から製品Aを取り出して出荷する必要があったにもかかわらず、製品倉庫2に置いてあった合格前の製品Aを取り出して出荷してしまった |
想定2では、作業者があるべき姿から異なってしまったのは「判断」のところからです。
想定では製品倉庫1には出荷前の製品が、製品倉庫2には合格前の製品が保管されているとしています。当然合格している製品を出荷する必要がありますが、作業者が知らなかったもしくは理解していなかった場合には起こりうる想定です。
もちろん出荷が作業者のみで実施するのではなく、QA(Quality Assurance、品質保証)部門が関係するとは思います。しかし、作業が形骸化している場合などでは起こりうることです。
まず、作業者には製品倉庫1からのみ出荷できることを教育しなければなりません。そして、製品倉庫2に置いてあるものは合格が出ていない製品であることを理解してもらいます。
その他は、行動でのミスについて対策します。
・正しい判断ができるように教育を実施する。
・正しい判断を妨げる要因を排除する。
想定3
認知 | 判断 | 行動 | |
---|---|---|---|
あるべき姿 | 製品Aの出荷があることを認知する | 製品倉庫1から製品Aを取り出すして出荷する必要があると判断する | 製品倉庫1から製品Aを取り出して出荷する |
作業者 | 製品Cの出荷があることを認知する | 製品倉庫1から製品Cを取り出して出荷する必要があると判断する | 製品倉庫1から製品Aを取り出して出荷する必要があったにもかかわらず、製品Cを取り出して出荷してしまった |
想定3では、作業者があるべき姿から異なってしまったのは「認知」のところからです。
口頭での指示や指示の記載を誤った場合に起こりうる想定です。口頭での指示によるミスの場合は「言った」「言っていない」の水掛け論になることが多いため、口頭での指示は無くすか注意を払う必要があります。
たとえば指示した内容を復唱してもらい、伝わっていることを確認するなどが必要となります。
指示書などへの記載ミスにも注意が必要です。
システム化できれば良いのかもしれませんが、どのみち「人」が介在するためミスが起こる可能性は残ります。またそもそも作業者が製品Aを知らずに、もしくは忘れていて製品Cと認知する場合もあります。
たとえば久しぶりに出荷する製品の場合には、注意事項として「製品Cと間違えないようにすること」などの記載も良いかもしれません。
最後に
ミスが人的要因に起因しているとしてもある程度の対策は可能であり、責任転嫁することなく対応することが必要です。
故意に引き起こされる異常は論外ですが、ほとんどの異常は結果として現れてしまったもので、意図して起こる訳ではありません。
「罪を憎んで人を憎まず」
みなさんの職場がより良くなることを願っています。